Rick O'Ryan
Introduced to woodturning at the age of ten, this form of creative expression has stayed with me, on and off for the past sixty years. I took shop classes in grades 7 through 9 back in Virginia to use the school lathes as they were better than the one I had at home. Early projects back in the 60s and 70s were primarily lamps.
Prior to moving to New Mexico in 1991, I was an active member of the Front Range Woodturners in Colorado, and I contributed to the successful start-up of that group. I demonstrated lamp and plate making, hollow vessel turning, and gave a slide presentation on the various cell structures used in microscopic wood identification. I have studied and photographed microscopic cell structures in order to understand and expose the macroscopic features I like in a finished piece.
In 1989 I attended a woodturning symposium in Utah, and met some accomplished folks who inspired me to try new directions. I was introduced to green wood turning, and to hollowing wood into vessel forms, boxes, and bowls. The advantage of turning wood when it is green, or fresh off the tree, is that it is easier to cut, and can be given a rough shape and hollowed, then set aside to dry. This results in much less loss due to cracking. Cracking happens when the inside part of the wood is still swollen and wet, but the outside has started to dry, shrink, and crack. Plus, it is great fun to spin green wood and watch the shavings pile up.
As I learned green turning techniques, my attention focused closer to home for sources of wood. Having worked with dried domestic and imported timbers for years, the change to local sources was welcome. Windfalls, firewood piles, and deals with tree trimmers and other turners have turned up some fine pieces that are a treat to open up and expose the beauty within. Consequently my wood collection evolved from stacks of lumber to sometimes include barrels filled with water containing submerged pieces of green wood that had been trimmed to turning size. This would prevent their degradation due to uneven drying. Some woods, like Russian olive, developed a nasty odor from being submerged in water, but most were not affected that way. Many of my hollow vessels were modeled after memories of southwestern shapes. When good fortune came my way and I acquired green wood, I would mow through those pieces, rough turn vessels, and stack them in the work in process area to dry. Rough turnings from years ago piled up with the stacks of lumber that these days don’t see as much attention.
Around ten years ago, I visited the old hospital at Ft. Bayard near Silver City, NM. The hospital was being demolished and many parts of the building were out on the lawn and were being sold off by the demolition contractor. I picked up a couple of buckets of fire suppression sprinkler heads. These started me down the road of making things related to fire fighting, such as miniature hydrants. The hydrants started out as whimsical and with no particular design in mind. After a number of those, I started making models of different versions of real fire hydrants, as close to scale as I could. These were all miniatures, and some of them could be used for opening bottles. Then, to keep making things more complicated, I moved on to hydrant lamps.
My finishes are primarily penetrating oils such as tung and urethane oil blends. Some of the softer, lighter color woods will get a clear lacquer finish penetrating beneath the wood surface to set the color with as little change as possible, and to firm up the wood for ease of sanding and subsequent finishing. I use no stains or dyes, though I often do add some tint to the resin when casting wood with voids. I also use stabilizing resin to firm up rotten wood as well as pine cone cores.
For occasional cleaning, wipe the piece with a soft rag moistened with lemon oil or a furniture cleaner. As with any wood product of this nature, do not expose to direct sunlight.
Other than the lamps, please pick up these pieces and handle them to help form your own impression of their weight and balance. The bottom of each piece is finished, numbered, dated and signed. Thanks for your appreciation of my work; I trust that your choice will continue to please you through the years.
Exhibitions
1991-1995 Adobe Patio Gallery, Mesilla, NM
1992-1994 StudioW, El Paso, TX
1992 Mimbres Region Arts Council, Imagenes de Luz
1993 WNMU McCray Gallery
1993-1994 Clifton Train Depot Gallery
1994 Poudre Valley Art League 33rd Art Exhibition Second Prize
1994-1996 Whipples Art Gallery, Silver City, NM
1994 AAW National Symposium, Ft. Collins, CO – demo on hollow vessels
1994 Johnson Gallery, Bisbee, AZ
1999 Governor’s Gallery, Timber Exhibition
2005 Glenwood Red Dessert Social
2005 WNMU Museum Employee’s “Discovered” Show, Best in Show in Wood
2006 Mimbres Region Arts Council members show
2007 Mimbres Region Arts Council Hot Art, Best in Show with Jim Pepperl
2015 Common Ground Gallery, Silver City, NM
2016 Silver City Public Library display
2018-2021 Encore, Silver City, NM
2018-2020 Sterling Fine Art, Silver City, NM
2023-present The Curious Otter, Lake Placid, NY
2024-present Sterling Fine Art, Silver City, NM
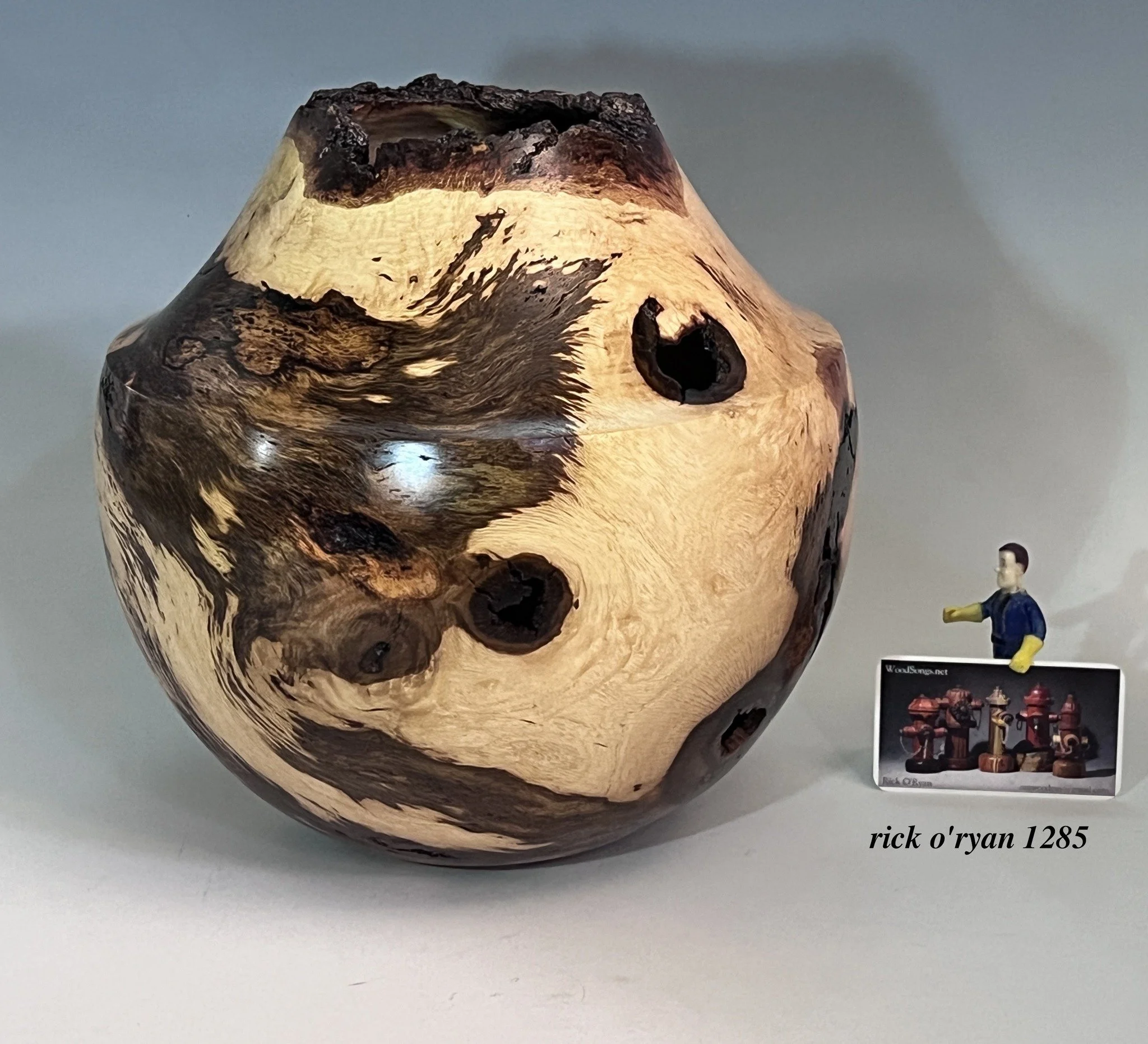
No. 1285
Rough turned on Jan 9, 1992 and set aside to dry. Finished Nov 2023. It’s a thin ¼” on the sides, and thicker at the upper part of the bark rim to display more of the bark. I am almost out of the oak pieces I rough turned in the early 90s, with just a couple of very small ones left. I hope there’s another big one hidden in the trailer but I don’t think that’s likely. I no longer have a source for these. I had marked on the rough piece the date, and that the rough turn and hollowing took 3 hours. I don’t recall the rough turning process taking that long for most pieces, so something with this one presented difficulty and I wanted to make note of that. Or perhaps I was just extra careful to not lose this piece. Gray oak, 10-1/4 x 10-1/2 x ¼in. $950.

No. 1285 (second image)

No. 681
There was very little moisture left in this oak tree when it finally succumbed to the wind and gave up its tenuous grip in the sandy soil of a wash. Out on a firewood expedition with a dead and down permit, my friend Jim Pepperl found this treasure of a tree. He was excited at the large growth near the base of the tree. “It was big,” he said. I pressed for a joint expedition out to see it. I did not hear back until one day I found out Jim had already retrieved the tree. He related his disappointment that the burl at the base of the tree would be of no use – it was hollow and rotten. He had already cut up the rest of the tree for firewood, but had saved this piece for joint contemplation of the extent of its rot. I asked if I
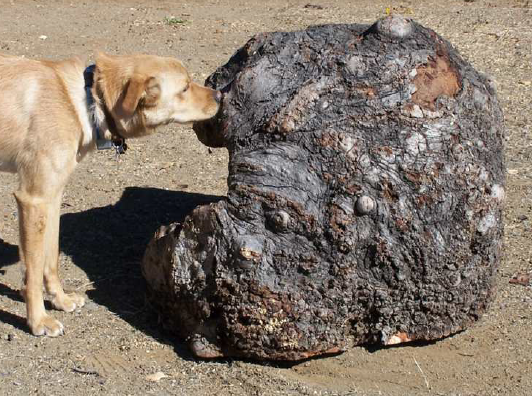
No. 681 (second image)
Here Rosie is telling me that if I don’t do something with it, she wants it.. After lots of measuring and some chain saw guess work and a boat load of resins to firm up the rot, it made it to the lathe. Then more resins as I uncovered more rot. My goal was to have none of the resin be visible. Somehow, it stayed together. The bottom is inverted to stay securely on the dome on top of Jim’s forged steel base.

No. 681 (third image)
Charlie adopted the Ten bowl as his place to chill. I thought, this might not end well. One day, he vigorously jumped out of it and sent the bowl to the floor. I took full responsibility for I had already had the vision of this happening. I kept it bunjeed in place with the blanket in it for Charlie until it was time to to apply more resin… after what was already in it, what’s a little more? It had became Charlie’s Ten bowl. However, once I had addressed the issue he had caused, he was no longer allowed in it.
Finished with wipe on polyurethane, then with a tung and urethane oil blend. 24.5” in diameter, 13.25” high, and it weights 45 lbs. On Jim’s stand, the top of the bowl is 46” off the floor. $6500.
No. 1253
A dozen or so years ago, the village of Tyrone cleared some Russian Olive trees and I was able to get a couple pieces. This is a crotch from one of those trees. I rough turned and hollowed it in 2006. The main single trunk below, pith included, splits into two branches. Those branches are visible on the left and right sides. The bark void is characteristic of the crotch area between branches. I wanted to retain the bark as best I could, knowing that as I hollowed behind it, a hole would open up, so I saturated the bark with ca glue. I could not get far enough into this with the 1" bar that came with my Kobra hollowing system, so I had to use the one from Lyle Jamieson's captured arm system. Then I had to make a different holder for the camera on the Bosch Visualizer to get it out further to be above the cutting tip, 10-3/4 x 15-3/4in. $730
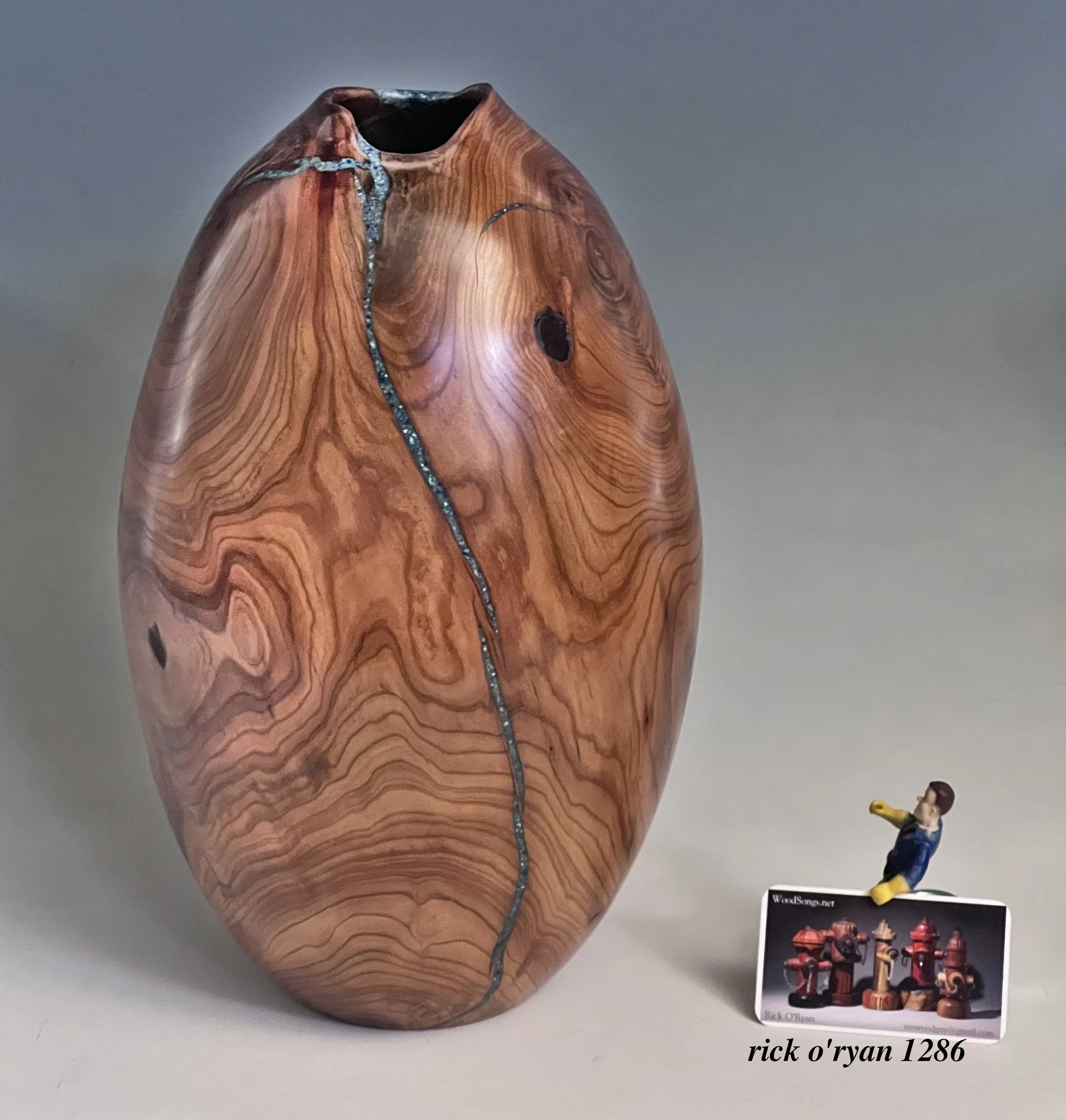
No. 1286
I helped Gene and Phyllis Jacobs for close to 30 years, with workstation and network issues at their title company business. I left when network technologies passed me by… Back in 2004, Gene took me out to Hurley, NM to his childhood home. There was an apricot tree at that house, that Gene had climbed in as a kid. The tree had been taken down and the current owner made Gene welcome to come get some of the wood. We selected a couple pieces. This one is a crotch from that tree. This cut shows the two branches at the top, and the main stem at the bottom. I rough turned it to approximately this shape, and set it aside to dry. During drying, a crack developed that ran the length of the piece. To keep it from exploding in the process of finish turning, I mixed some fine ground azurite in epoxy and pressed that into the full length of the crack and some more in the small divots left at the crotch when the bark broke off. With the epoxy in place, the sound this made as the tool was applied with the wood spinning no longer screamed of imminent danger, yet careful attention was called for, including standing outside the line of fire. 8 x 13 x ¼in. $1040.

No. 739
Back in the early 90s I started a planetary series with Saturn in mind. I rough turned nine pieces, because at the time Pluto was still a planet and in many of our minds it still is. I turned each of them on two axes, and carved off the material at the intersection of those axes. I knew that for the finishing process, after the pieces dried, that I would repeat using those two axes. I successfully finished eight of them, and sent one to another turner who finished it and sent it back to me. This is one of the ones I finished... it is gray oak. $930.

No. 711
In the early 90s I started a planetary series with Saturn in mind, with a ring. I rough turned nine pieces, because at the time Pluto was still a planet and in many of our minds it still is. I turned each of them on two axes, and carved off the material at the intersection of those axes. For finishing, after the wood had dried, I repeated that process using those same two axes, as close as I could get to them. I finished eight of them, and sent one to another turner who finished that one and sent it back to me. This is the sixth of the series, finished in 2013. The tannin swirl reminded me of a horse head. For this one, I removed the bark from the ring. which was facilitated by it being a spring cut. The darker neck inlay is from a tannin saturated part of the same wood. 8.7" at the largest diameter x 6.7" high. Finished with wipe on poly. Gray oak, Quercus grisea. $930.

No. 722
A study in tannin... the Lazy P in the middle was turned green, right off the tree, no treatment other than drying. The piece on the left was cut from the branch, then submerged in water for several years, with scrap steel in the water. The darker color is from the iron - tannin reaction. The piece on the left, and the one in the middle, are gone. The piece on the right, 722, was turned to finish, then fumigated over ammonium hydroxide, or anhydrous ammonia, for 24 hours. This is an ages old process used to darken white oak furniture, rather than using stain or dye. The ammonia reacts with the tannin and darkens the wood. No. $590
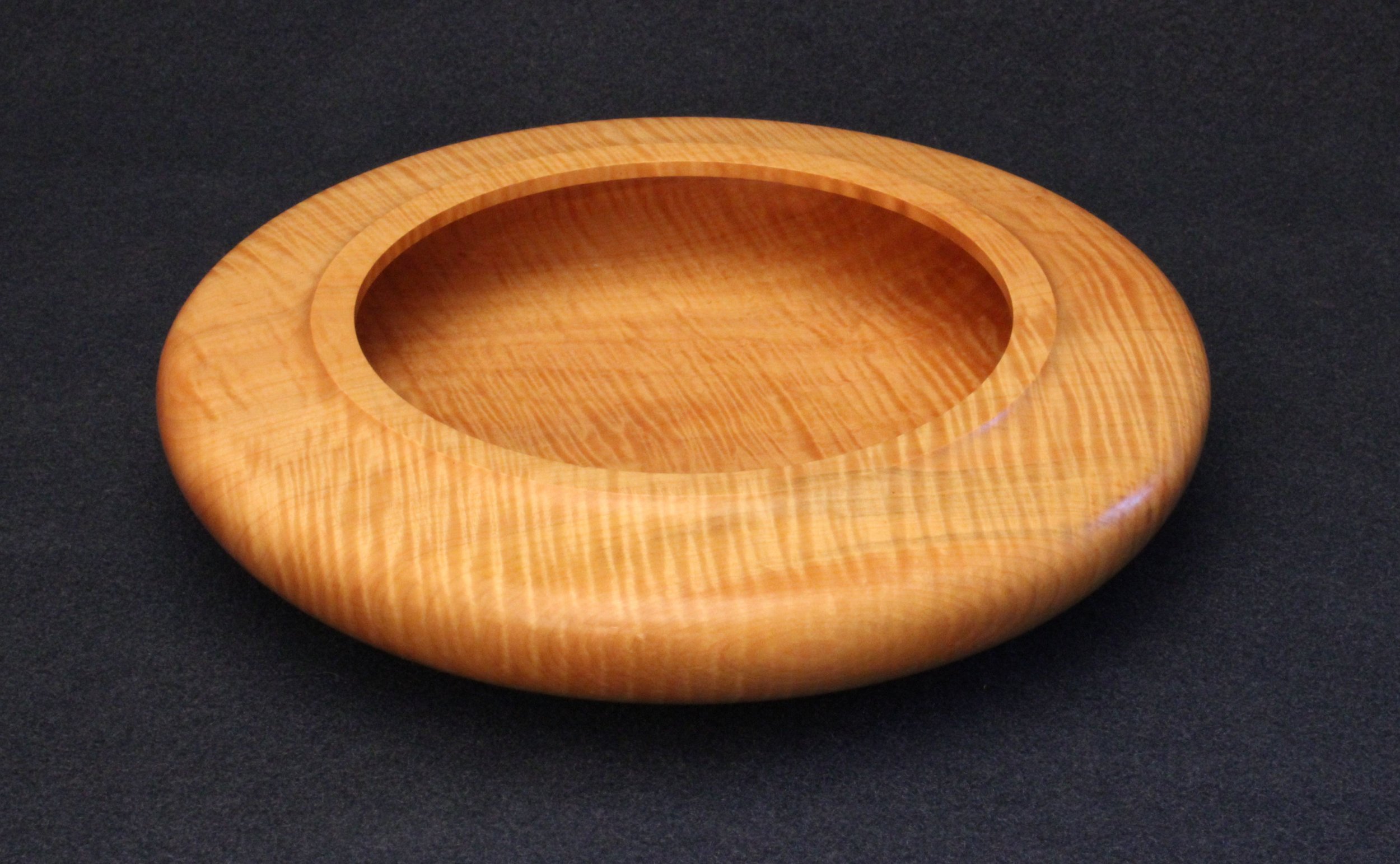
No. 570
Cleared by the City of Fort Collins, Colorado, back in the late 80s, this silver maple tree was dropped off at the Colorado State University wood lab. Parts of the tree exhibited a noticeable curl. I obtained this piece while attending a turned wooden lidded container workshop with Kip Christensen and Lee Carter in Ft. Collins.
This piece displays the nicest curl I have seen in silver maple. Curl of this quality comes at a price, and I was fortunate to get this piece. Note how light refraction changes as the piece is rotated. Like tiger eye stone, the bowl's surface has a three dimensional appearance.
This bowl with the large undercut rim has been in my own collection all this time, having made an appearance in Sterling in 2019. I had two more pieces of wood from that tree, one of which I made into a similar piece as this but it did not have as distinct a curl. I decided it’s time to offer it up. $770
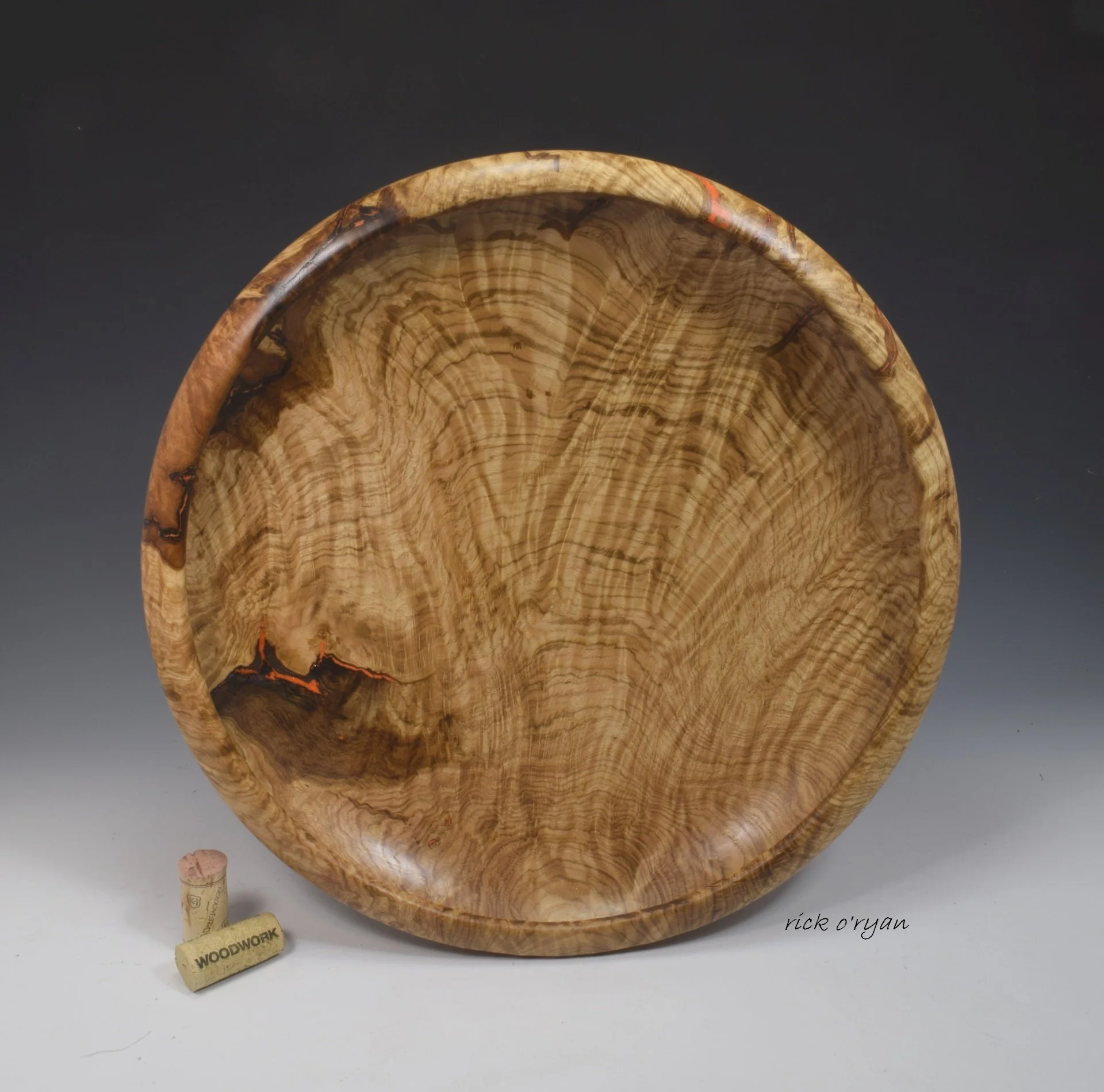
No. 814
Gambel oak, collected on a firewood permit from the 2014 Signal Peak fire area. Turned green, allowed to dry and move. I then filled with resin and leveled the crack inside, and sanded the inside smooth. I chose a red tint to the resin to suggest the fire around this tree. The bottom is still quite textured from the movement along the curls of the wood in this crotch area between the two trunks of the tree. The movement of the wood during drying can be felt along the rim. Tung oil finish, 13-7/8 x 2-11/16in. $630
No. 1247
Second mesquite in this series of six oak and three mesquite pieces that I started 30+ years ago. The use of a tool that is new to me has made it fun to do these again. The process of connecting with my thoughts and intuitions of three decades ago has been tickling my fancy. It has also been fun to work on pieces that can be "finished" in a day, as opposed to the 50 or so hours that I put in a hydrant lamp.. That "day", of course, does not include the gathering of the wood, the rough shaping and hollowing process, nor the oiling and additional sanding and polishing that inevitably follows the lathe work. 8-1/2 x 3 x 3/16". The camera shutter could not wait for fire guy holding the business card to make it into the pic in time. $550
No. 1250
Cleared by the City of Fort Collins, Colorado, back in the late 80s, this silver maple tree was dropped off at the Colorado State University wood lab. Parts of the tree exhibited a noticeable curl. I obtained three pieces from this tree while attending a turned wooden lidded container workshop with Kip Christensen and Lee Carter in Ft. Collins.
The three pieces displayed varying degrees of curl. The first one I finished back in the early 90s and recently I finished the other two.. Note how light refraction changes as the piece is rotated. Like tiger eye stone, the bowl's surface has a three dimensional appearance.
This one is slightly larger than the one I finished back in the 90s, 14-3/4 x 2-7/8 x ¼in. $570
No. 1256
The character in this burl is unusual in the pieces I have come across. It is more characteristic of burls in the midwest. This is some species of oak, I suspect Gambel, but unlike most of the pieces I rough turn and hollow, I write the species and the date on it. Not this one. So it was a mystery to me. But I sure like the character of the eyes in this burl, 8-5/8 x 6-3/4in. $770
No. 1258
Cleared by the City of Fort Collins, Colorado, back in the late 80s, this silver maple tree was dropped off at the Colorado State University wood lab. Parts of the tree exhibited a noticeable curl. I obtained three pieces from this tree while attending a turned wooden lidded container workshop with Kip Christensen and Lee Carter in Ft. Collins.
The three pieces displayed varying degrees of curl. The first one I finished back in the early 90s and recently I finished the other two.. Note how light refraction changes as the piece is rotated. Like tiger eye stone, the bowl's surface has a three dimensional appearance.
This one is slightly larger than the one I finished back in the 90s, 14-3/4 x 2-7/8 x ¼in. $570.
No. 1259
Rough turned and hollowed in July 1993, set aside to dry. Finished in July '23. Gray oak. In revisiting these works in progress, I try to see what I had in mind when I did the rough turning. Does the design I apparently had in mind still appeal to me, or could I impose something new to it? In most of these cases, I stick with what I still see in the rough turned piece. In this case, I did all I could to preserve the character of the opening at the top. When Gray oak forms this character it is one of my favorite woods to work with. The tree appears to send tannin to the injury and these swirls form where the tannin gets deposited. 7-1/2 x 7in. $550
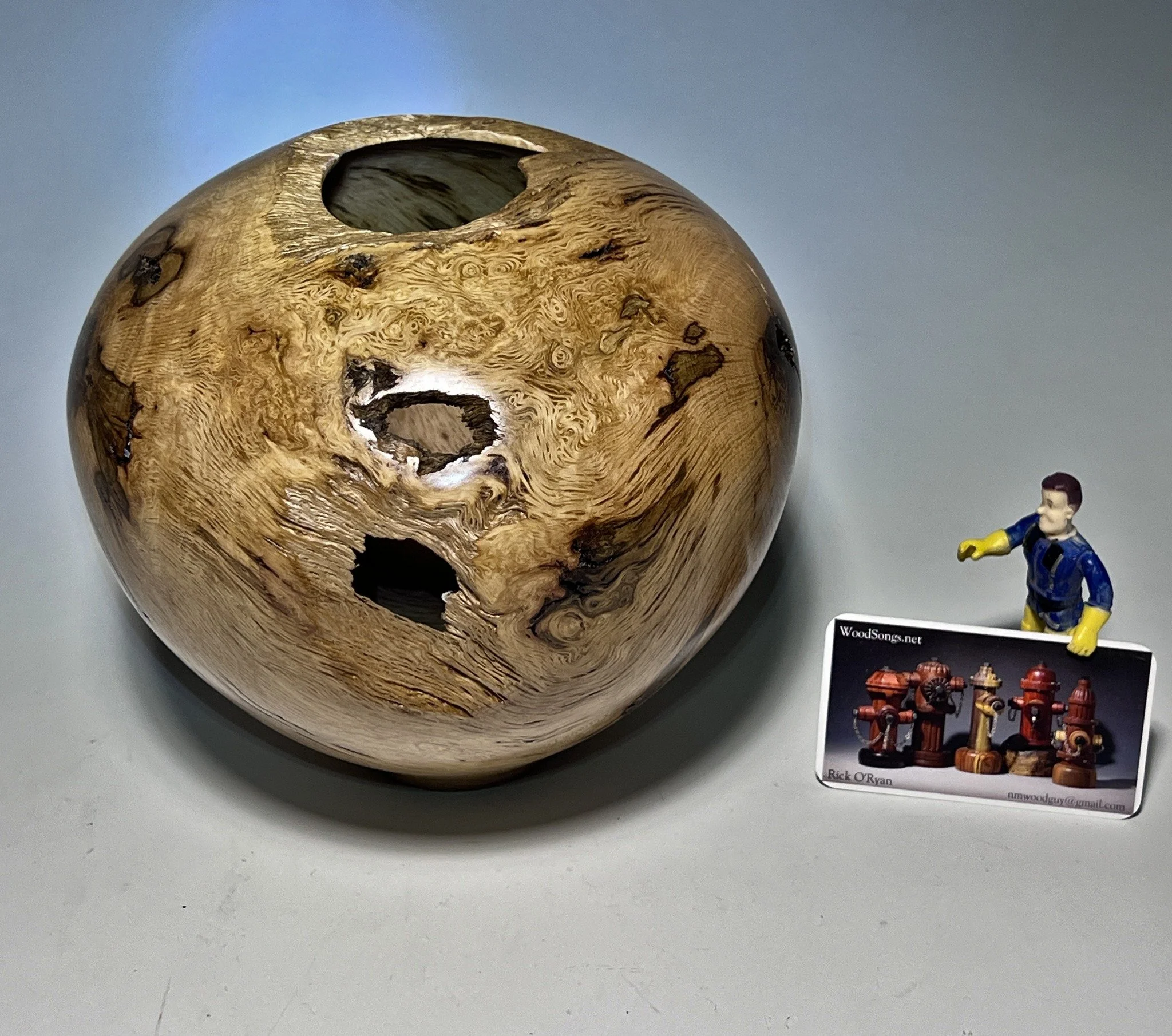
No. 1259 (second image)

No.1268
In 1990 I attended a lidded container workshop, hosted by Lee Carter, at CSU in Ft. Collins. Lee was doing research into bending wood after soaking it in Amway soap. I acquired three pieces of curly silver maple at that event, from a Ft. Collins city tree. This is the third and last piece, rough turned in August 1990. It's been dry, waiting for a finish turn for a few years... 8 x 5in. $440.
No. 1278
Back in May 1992, a Wisconsin friend of mine visited down here in southwest New Mexico. He was a wood worker, but not a wood turner, and I never expected him to become one as he had other interests. However, I prevailed upon him to get on the lathe and try his hand at rough turning two pieces of green wood into hollow vessels to prep them for drying. We worked on them together. The two pieces went back to WI with him, to end up forgotten in a cardboard box in his storage locker. On my recent trip to WI we found them in the locker and got a good laugh, and he said, these need to go back to NM with you. I agreed, and told him that he would get one of them back as a finished piece. This is gray oak, 6-5/8 x 7-1/4 x 1/4in. $560.
No. 1281
The sound of a chainsaw gets my attention, whether it is being used for constructive, or destructive purposes. I heard one being used in downtown Silver City, back in 1992, on an ash tree at 505 W. College Ave, which has Smith Real Estate as its current occupant,. The tree being cut had some rot at the base, hence the decision to bring it down. I offered to help, if I could collect several pieces of the wood. This came from that tree, and was rough turned in 1992 and set aside to dry. 6-1/4 x 5-3/4 x ¼in. $390.

No. 1282
Back in the 90s I got some mesquite but did not care well for the raw wood, which ended up in my firewood pile. Most of the wood I got back then went into water barrels until such time as I could work with it - but not so this piece. After years in the burn pile, I salvaged it, as faulty as it was, as I could not bear to burn it. At some point between then and now, I turned a shape on the outside, and since it was already dry, I did not bother to hollow it, and left it in my pile of work in process. In 2023 the squirrel that got my attention was this one, so I finished the outside, and hollowed it. Some ca glue helped keep parts of this from breaking loose. Like much of the wood I work with, it's best to not stand in the line of fire when the wood is spinning. 7-1/2 x 7-7/8 x 1/4in. $740.
No. 1291
The second of the four areas of interest in the long dead and dry oak I recently acquired. I wish there had been enough material around it to identify the species. In the area are gray, emory, and a few gambel oak. There may be others scattered but based on the wood alone, I can't tell which it is. Like the one before, and both that will follow this post, it was a challenge to work with this knowing it could fly apart with any tool catch, or even without. This one ended up being the thinnest wall of the four, at 8-1/4 x 7-1/8 x 3/16in. Thin was not my goal - balance, and keeping the piece intact were my goals. It has a tung and urethane oil finish. $750
No. 1292
The third, and largest, in the set of four made from a long dead and mostly dry oak branch. Much of the exposed wood on this branch had been bleached by the sun to barnwood gray. It is 13 x 17 x 3/8in and it presented the biggest danger of coming apart. Hollowing the inside was hairy... there were four larvae and at least 27 ants that came out of it, not counting the ones made indistinguishable by the cutting tips. The chickens got the two big larvae. It stands 17in high, and measures 15-1/4 down to the inside bottom. Underneath, I concave cut the bottom of the base so that there was about 1" of material at the center of the bottom. I usually try to make that thickness at the center of the base the same as the walls, but for this one I wanted a little more weight at the base for stability, and because I chose not to press my luck. Finished with a tung and urethane oil blend. $1250
No. 1292 (second image)
No. 1293
The last of this set of four vessels made from a long dead and dry oak branch. The branch may have been discarded by firewood folks long ago. Since the wood was dry, hollowing was quite a challenge due to the preponderance of faults, cracks and voids. But, all four held together. Note on the lower left where the branch entered, and on the upper right where it exited. Unfortunately there was no material from which I could identify the species of oak. 8-3/4 x 7-1/4 x ¼in. Finished with a tung and urethane oil blend. $740.
No. 1294
Thirty years ago, in March 1994, I got this apricot from a tree on Romero St, in Hurley, NM. It was a crotch, already split as the tree had died. I knew each step of this one would be a risk and require techniques I would have to make up as I went. A filler in the cracks by itself does not make a strong bond, so this would require extra attention. During the rough turning, I had it wrapped with glass fiber and epoxy. For the finished crack, I did not want to do bowties or stitches across the gaps so I put a ballon inside, and filled the crack with azurite and first epoxy, then finished it off with ca glue. I made an aluminum ring for the neck, and fitted and glued that in place before the apricot burl neck went over the ring. The neck is from a small apricot burl I acquired much more recently and subsequently used for some bolos. 7 x 11-3/4in. $740.
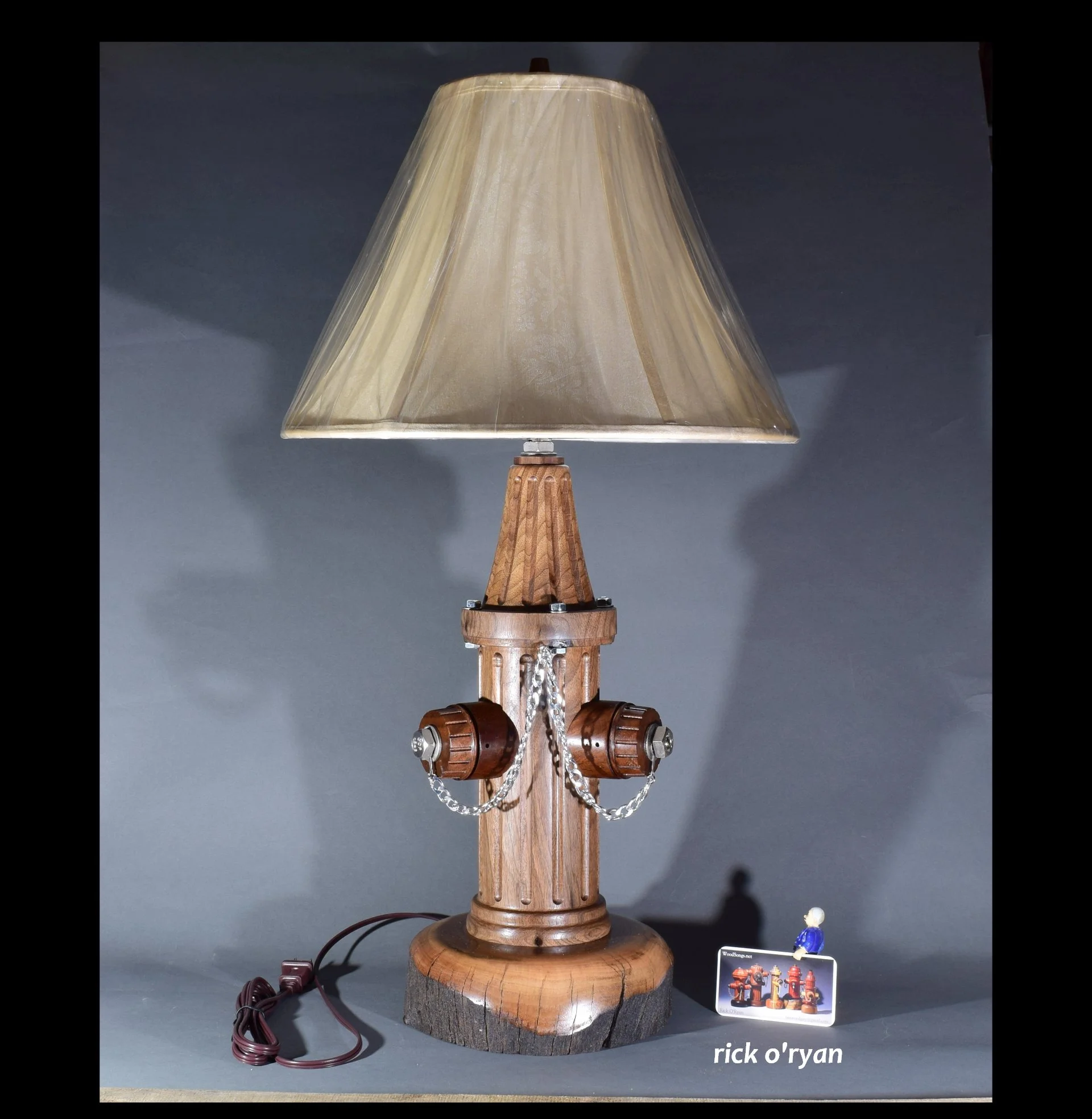
No. 1097
The Crayon. This is my Arizona walnut (native to NM) interpretation of a circa 1905 "Standard" hydrant by the Crane Co, Chicago. The light switch is in the right port but at the request of a lefty I can move it to the left hose port. The penta-bolts are salvage, from an ebay store. Two of them are converted into penta-nuts. The penta-nut on the power switch has a set screw gripping the head of the rotary switch. There is a walnut octo-washer on top of the bonnet, under the top penta-nut. The piece serving as a chain hanger under the bonnet flange is salvage from a bike chain. 8-5/8” diameter, x 16-3/4in to the base of the harp. $1490
Plus optional shade at $112.50.
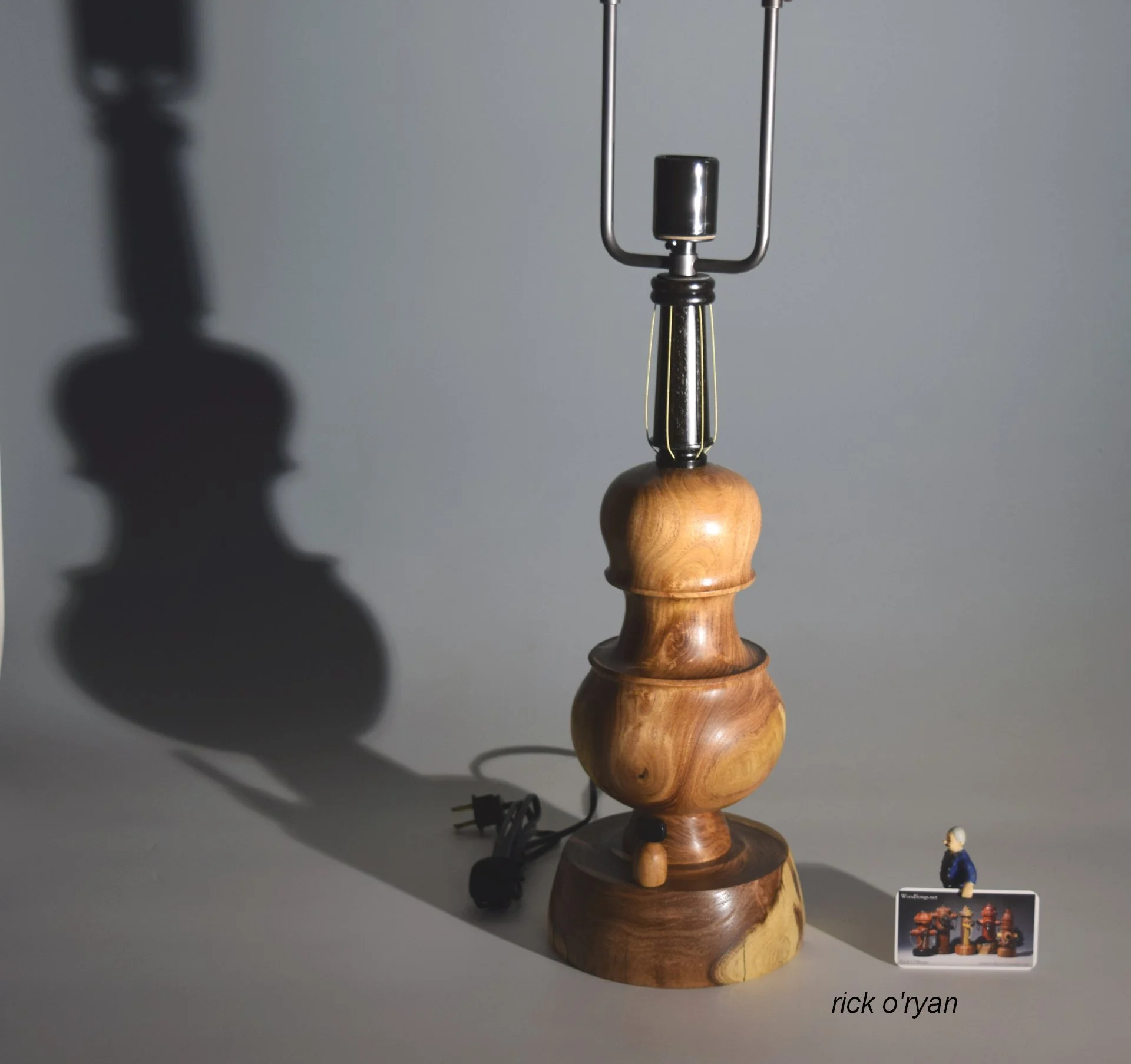
No. 1107
Back in the 1970s and 80s, I made a half dozen or so lamps in the style of a fiddle in the round, most with strings. A regular customer of mine dubbed these as mello cellos. I know the whereabouts of only two of the old ones from the 70s, and one of those has strings. I've always liked the design, so I decided to make some more. What's a 4 decade gap, anyway. I did do a couple of bottle openers in this style, no strings, but they did not have the complexity of the lamps. Fortunately I have found quality hardware so I'm not limited to the Leviton stuff I used to use. When I find quality hardware, if I need one for a current project, I tend to buy twenty to get a price break. So that means lamps are here to stay for a while, either hydrant, or fiddles. This one that takes the 43 year hand off is mesquite, with African blackwood (a rosewood) for the neck. I used ukulele pegs for the finial and the switch. It stands 16-7/8 to the base of the harp. No. 1107. Some folks have had trouble making the jump from a fiddle to one in the round, so for them, I say, look at the shadow. $1490
Plus $112.50 for the optional shade.

No. 1110
The first three lamps I made in 2021 were in the “fiddle in the round theme”, and are basically similar to the first fiddle lamp series I did 40+ years ago, with, of course, minor differences. This one is the fourth in this series and has a significant change. There are four strings, ranging from 62 gauge to 24 gauge (guitar strings use a different gauge definition than other wires), and they extend below the neck across the waist and are attached to the lower belly. This one is a mesquite and steel stand up bass for a gear head. The bolt hardware is stainless steel from the inventory of an old airplane mechanic who is no longer with us. The bolts have a hole through the thread area, so four of them became tuning pegs. It would seem that the holes in the threaded end of the bolt are for security wires so their nuts don't get lost if they vibrate loose. The steel forged disc is from the scrap collection of my blacksmith friend JP, as is the pipe that serves as an end pin under the bottom belly. The pipe is welded to the disc on the under side and the disc is bolted down into the base. To maintain the right distance between the string and the neck, the neck is bigger in diameter on its lower end than the previous lamps, and I cut flats on the upper belly to clear the strings. I could have shaved a flat off the back of the neck, but did not think of it. Do not pluck the strings, this is not a musical instrument. If the strings come loose from being plucked, the repair is extensive and I'm not even sure how I would do it. 6" in diameter at the base, and stands 20-3/4in high to the bottom of the harp. The harp has 4in vertical adjustment range to facilitate fitting a shade. The switch has a bolt head on top, as does the finial. I enjoy setting the lighting up to feature the shadow. $1490, without shade.
No. 1152
This is my interpretation of the Mueller wet barrel, LA Sleeve Van Deventer style single port hydrant. A wet barrel hydrant is sometimes used in locations that do not experience frost, and is always charged with water under pressure. A hose port on one side of the barrel will have a valve to control that nozzle on the opposite side of the barrel. This is blistered red maple from Wisconsin. I gave the port cap and the valve body some extra character with a burr bit on a flex shaft carving tool. The lamp switch is the penta-bolt head on the valve body opposite the hose port. Base 7in diameter, stands 15-1/2in tall to the base of the harp. $1490.
An optional shade may be selected from one of the other lamps, or may be acquired from the shade source of your choosing.
No. 1170
The Daigle D67M fire hydrant with two hose nozzles, or ports, was made by Concord, in Canada, now known as Clow Canada. This is a choice hard maple burl with a void up one side. To fill the void, I cast the cylinder in a mold. with red tinted chilepox – red chile flakes in epoxy casting resin. For the base, no tint, just chilepox. If the red streak up the side makes you think of fire, it's a good thing your lamp is a hydrant. The switch is in the right nozzle, but for a lefty it can be moved to the left port. The base is 5-3/4in diameter and the lamp stands 15-1/8in to the base of the harp. The harp has close to 4in of vertical travel for flexibility in choosing a shade. $1490 without shade.
An optional shade can be selected from one of the other lamps, or from a shade source of your choosing.
http://www.firehydrant.org/pictures/clow-canada-daigle-concord.html
No. 1174
Mesquite, from Oro Valley, AZ. This hydrant lamp is modeled after the Mueller Super Centurion, made in Alabama. The bottom flange, barrel, top flange and bonnet are all one piece, no joints. With the two hose ports, the two pieces in the pumper port, the penta bolt heads on the port caps, the penta washer above the bonnet, the penta bolt finial, and the false bottom, there are eleven pieces of wood. The base is 6" diameter, and the lamp stands 14-1/2in to the base of the adjustable harp. The harp has close to 4in of adjustment to match a desired shade. The lamp switch is in the pumper port cap. $1600
The optional shade is from LampsUSA, $157.50.
No. 1176
Emory oak, of the red oak group. The tree had rot at the base, which caused it to come down. There are some real nice colors near that rot. The emory oak is the large, semi live oak in the Burro Mountains, the southwest part of the Gila National Forest. There were many faults and cracks, so after drying it the rest of the way, I cast this in epoxy casting resin. My intent was to not feature the resin, and have it blend in with the colors in the wood. This hydrant is modeled after a design produced by Glamorgan Works, of Lynchburg, VA, which was patented in 1897. The base is 5-1/2in diameter, and 13-3/8in to the base of the harp. It is 8in across the port cap nuts. The lamp switch is in the right port, activated by the port "penta-bolt head". For a lefty I can move the switch to the left port. $1490.
The “Copper Empire Mystic Topaz” shade is from JustShadesNY, $275.
http://www.firehydrant.org/pictures/glamorgan-pipe+foundry.html
No. 1180
It's only an urn if cremains are what you put in it. Otherwise, it's an impractical box, or simply a fun, hollow, standalone model of an antique hydrant. It's an interpretation, with turners license, of the 1880s Ludlow List 75 hydrant. I was asked a while back if I had done, or could do, an urn, with 30-50 cu in capacity, and one day I may do one that size. I got out of control with this and went bigger. This is apricot, on an Arizona walnut base. The access is the funnel ready 3/4" valve control rod hole in the bonnet. The hole is tapped to 3/4-10 threads and has a penta-bolt with helicoil bringing it up to that size. Internal capacity is around 130 cu in. The base is 7-1/8in diameter and the piece stands 18in tall, with around 8" across the port caps. The base is a round from a dead branch, with multiple cracks and rot. Some epoxy in the cracks, and thin ca on the rot, and it is solid. I hollowed the base and cut the bottom out of the hydrant, making it a “pipe” so that added to the internal capacity. $1600.
No. 1180 (second image)
No. 1186
This is my Arizona walnut impression of a Traverse City (Michigan) Iron Works hydrant. This one is the Mae West version with just two hose ports. The lamp switch is in the right port cap, though for a lefty I can move it to the left port. This wood came from the standing dead part of a tree and was quite faulty and took some resin to fill the cracks. This had some nice crotch figure toward the outside of the cylinder I started with. That character changed some as I cut in, and contrary to a habit I like to stick to, I cut flutes into the active grain so one must look harder to see it. The base is 6-1/4in diameter, and the lamp stands 18in to the base of the harp. $1490
Shade is optional.
No. 1189
A mesquite interpretation of the RD Wood / Mathews tall bonnet model hydrant, made by Kennedy Valve Co after they bought out RD Wood. There was a variety of tall bonnet versions made; this one is from around 1962 and has fluting all the way up the bonnet. This measures 9in across the hose ports, and stands 14-7/8in to the base of the lamp harp. The switch is actuated by turning the pentanut on the pumper port cap. $1600
Optional shade $112.50.
No. 1190
This is my apricot interpretation of the Kennedy K21 hydrant. I cast the very faulty, old, dry, cracked, discarded by someone else, apricot crotch cylinder in epoxy resin, with a little blue in the resin. I did not want to feature the resin very much, and, most of it ended up on the shop floor. The exception was a crack in the base which did not fill with casting resin. So there I brought out the color, with the same blue chalk line powder set with ca glue. It's 8in across the ports, and stands 15-1/2in to the base of the harp. The switch is in the right port, but for a lefty I can move it to the left port. $1490
Optional shade $112.50.
No. 1238
This is a lamp for a conehead. It’s a large Coulter pine cone from California, a lot of urethane casting resin, and an Arizona walnut base. It has a touch sensitive switch to turn on the bulb. The harp has 4" of travel for vertical adjustment to fit a shade. Base is 7" diameter and the lamp stands 15-1/8" to the base of the harp. Around eight years ago I bought a number of Coulter cones, along with chir and Jeffrey cones from an ebay store that operated out of southern California. I cast this cone with a little red tint in the urethane casting resin. The resin was not a deep pour resin but I got away with it. The riser just below the harp, and the finial, are from the core of a smaller Coulter cone. $1600
Optional shade, $112.50.